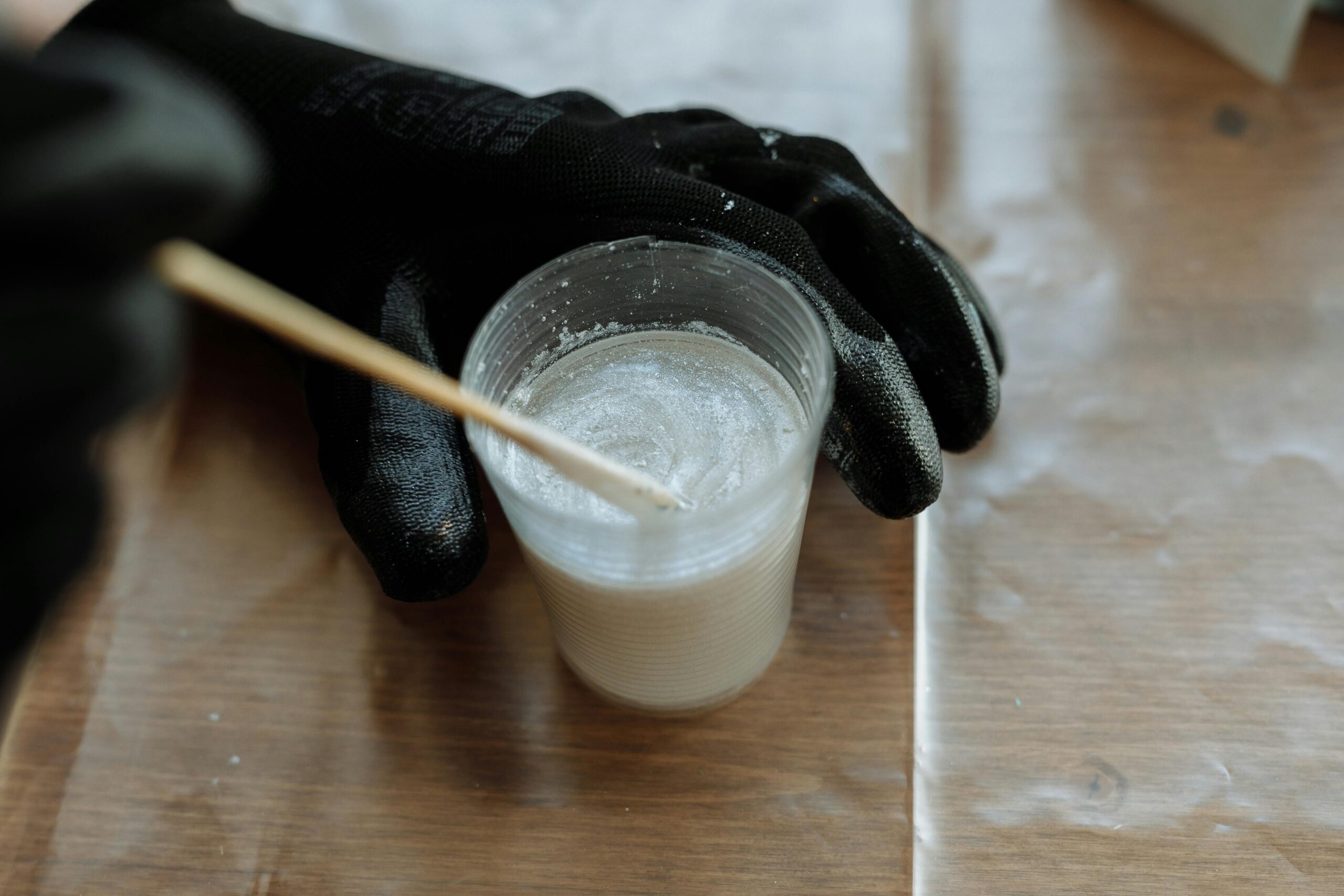
Embarking on a journey with epoxy resin offers a pathway to unleash creative potential through crafting stunning, durable finishes on an array of projects. It’s a versatile medium favored for its high gloss, strong adhesion, and protective qualities. Before you dive into mixing and applying epoxy resin, understanding the fundamentals and honing your measuring and mixing skills is critical. This guide aims to equip beginners with the knowledge and techniques to handle epoxy resin with the same finesse as a seasoned professional.
Gaining proficiency in the art of working with epoxy resin is not just about following steps; it’s about embracing a meticulous and patient approach. Each stage, from preparation to finishing touches, holds significance in achieving your desired outcome. As this guide unfolds, you’ll learn the nuances of resin work, ensuring that every pour and polish contributes to a masterpiece you can be proud of. Let’s embark on this transformative journey, turning the complex into achievable, one meticulous mix at a time.
Understanding Epoxy Resin
Epoxy resin is a term that encapsulates a world of possibilities, referring specifically to a two-part system comprised of the resin itself and a hardener. When these parts are mixed, they undergo a chemical reaction that transforms them into a rigid, plastic-like material. With applications that range from crafting to construction, this compound is celebrated for its versatility and strength. For beginners, it’s paramount to understand that the properties of epoxy can significantly vary; hence, selecting the right type for your project is the foundation of success.
There are epoxy resin types tailored to different applications: some cure to crystal-clear finishes ideal for jewelry or tabletops, while others are engineered for enhanced resistance to heat and chemicals, suitable for industrial use. The working time—or pot life—temperature resistance, and viscosity are factors that can influence your project. Beginners should aim for user-friendly resins that offer adequate working time and straightforward mixing ratios. By comprehending the basics of epoxy resin, crafting bespoke pieces with durability and aesthetic appeal becomes not just an ambition, but an attainable reality.
Safety Measures
Dealing with chemicals like epoxy resin requires strict adherence to safety protocols to ensure a hazard-free crafting experience. The foremost precaution is to don personal protective equipment (PPE) before starting your project. This includes wearing gloves to protect your skin, a mask to prevent inhalation of fumes, and safety goggles to shield your eyes. Exposure to the components can lead to skin irritation or allergic reactions, and the fumes can be especially harmful if inhaled in an inadequately ventilated area.
Furthermore, ensuring your workspace is well-ventilated is crucial to maintaining a safe environment. An open window, a fan, or even working outdoors can be effective means to disperse any potentially harmful vapors. Additionally, keep your area clean and organized to prevent accidental spills or contamination, and always have a spill kit with substances like vinegar or alcohol ready to manage any mishaps. By respecting these safety measures, you’ll create a responsible practice that prioritizes your well-being, allowing you to focus on mastering the craft of epoxy resin.
Tools and Materials
Before delving into the hands-on process of epoxy resin work, assembling the right tools and materials is essential. For precise measuring and mixing, you will need clean, dry mixing cups marked with volume measurements, stirring sticks, and a digital scale—an indispensable tool for guaranteeing accuracy. The type of scale you choose should have the capacity to measure small increments, ensuring the resin-to-hardener ratio is exact.
Selecting high-quality materials relevant to your particular project also plays a significant role in the outcome. The surface you plan to work on, whether it’s wood, canvas, or metal, should be prepared accordingly, and the choice of resin should align with your project’s final requirements—be it transparency, color, or resistance to elements. Investing in proper tools and materials sets a reliable stage for your epoxy resin project. With these in place, there’s an assurance of efficiency and precision, laying down a solid foundation for success.
Measuring Epoxy Resin
Accurate measuring is the cornerstone of successfully working with epoxy resin, as the chemical process is reliant on a precise ratio of resin to hardener. Typically, these ratios are determined by volume or weight, with manufacturers providing the specific ratios for their products. When measuring by volume, use graduated mixing cups and ensure you fill to the exact markings for each component. A pro tip for clear measurements is to position your eye level with the measurement mark on the cup to avoid over or under-pouring due to perspective distortion.
Weighing by scale offers a higher degree of precision, particularly beneficial for large or critical projects. Turn on your digital scale, calibrate it to zero, and measure the resin first, followed by the hardener. Adhering to the exact weight ratio is vital; even a slight imbalance can result in the mixture not curing properly. Once you’ve mastered the measurement process, you’ll have a reliable base from which you can proceed to mix and ultimately, create with confidence.
Mixing Epoxy Resin
Mixing epoxy resin is more than simply combining components; it’s a meticulous process that, if done correctly, results in a flawless and effective cure. Begin by pouring the measured amounts of resin and hardener into a mixing container. Using a clean, flat stir stick, blend the mixture thoroughly, scraping the sides and bottom of the container as you go. Stir slowly but consistently to avoid introducing air into the mix, which can lead to unwanted bubbles. This process should generally take about 3 to 5 minutes, depending on the volume, but always refer to the product’s instructions for the best results.
A common issue to be wary of during mixing is an incomplete blend, which can cause soft spots in your finished product. To ensure a homogeneous mixture, some professionals recommend pouring the mixed resin into a second clean container and stirring again to catch any unmixed parts. Once fully mixed, the resin will start to cure, so time is of the essence. It’s recommended to plan your work in stages, mixing only what you can apply within the pot life of the resin. Properly mixed epoxy resin should be clear and streak-free, indicating it’s ready to be poured or applied as needed for your project.
Tips for a Bubble-Free Mixture
Achieving a bubble-free finish in epoxy resin projects can elevate the quality of the work, resulting in a piece that epitomizes professionalism. One of the key strategies to minimize bubble formation is by ensuring both components—the resin and the hardener—are at the recommended temperature before mixing. Often, warming the resin in a water bath to a mild temperature can reduce its viscosity, making it easier to mix thoroughly without entrapping air.
During the mixing process, mix slowly and deliberately. Rapid or vigorous stirring can introduce air, leading to bubble entrapment. After pouring your resin, gently touching the surface with a heat gun or propane torch can coax bubbles to rise and pop, but this should be done with cautious, sweeping motions to avoid overheating any area, which can cause scorching or warping. Pouring in layers is another effective technique, especially for thicker applications. Allow each layer to partially cure and release trapped air before adding the next. This deliberate approach ensures a professional, bubble-free finish, showcasing the true beauty and clarity of the epoxy resin.
Applying Epoxy Resin
The art of applying epoxy resin hinges upon precision and finesse. After thoroughly mixing, it’s important to immediately pour the resin onto your work surface to avoid premature curing in the mixing container. Pour in a steady, controlled manner to evenly coat the surface or fill the mold. If covering a surface, use a squeegee, brush, or roller to spread the resin to the edges, ensuring full and even coverage without introducing air bubbles.
Pay careful attention to the environment in which you’re working; dust and airborne particles can mar the surface of your project. Ideal conditions include a clean, dust-free space with controlled temperature and humidity. Gravity plays a crucial role in self-leveling resins, so confirm that your work surface is perfectly level before application. Once applied, the epoxy will begin its curing process, transforming from a liquid to a solid state. Curing times vary between products, and patience is essential here; allow the applied epoxy to rest undisturbed during this phase to ensure the best results. Proper application and environmental control allow the intrinsic properties of the epoxy resin to shine through, resulting in a project that not only looks professional but lasts.
Finishing Touches
The transition from a cured epoxy resin project to a polished end product involves several critical finishing steps. Sanding is often the first stage in this phase, beginning with coarse grit sandpaper to remove any major imperfections or uneven areas. This should be done with care to avoid creating scratches that are too deep to remove. Gradually move to finer grits until the surface becomes smooth to the touch. For a high-gloss finish, wet-sanding can be utilized, which helps to reduce dust and refine the surface further.
Buffing and polishing are the next steps to achieve that glass-like surface that is often desired in resin work. Using a polishing compound and a buffing machine can elevate the sheen to a professional standard. It’s also important to clean the surface between sanding and polishing to remove any residual dust or debris that could compromise the finish. The final touches bring the project to life, reflecting not just light and luster, but the care and attention invested throughout the creative process. With these meticulous processes, the project transcends its rudimentary state, revealing the depth and clarity that only well-applied epoxy resin can offer.
Troubleshooting Common Issues
Navigating the initial learning curve of epoxy resin work often involves tackling common challenges that can arise. Bubbles are a frequent concern and can be addressed with careful mixing and application techniques, as previously described. If you find soft or sticky spots on what should be a hard, cured surface, this typically indicates that the resin-to-hardener mixture was off-balance or not thoroughly mixed. Remedying this may involve removing the uncured areas and reapplying a fresh, correctly measured and mixed batch.
Another common issue is fisheyes, which are small craters or indentations that appear in the finish, often caused by surface contaminants like oils or dust. Clean the surface thoroughly before application to prevent this. If fisheyes occur, applying an additional thin coat of resin can cover them up. Furthermore, should you encounter colorants or additives that haven’t mixed well, remaining streaky or uneven, ensure that these are compatible with your epoxy system and that you’ve followed the recommended guidelines for their inclusion.
By confronting these obstacles with informed solutions, you can refine your technique with each project. Remember that many issues have simple solutions, and with practice, preventing and fixing these mishaps will become second nature.
Key Takeaway
Embarking on the journey of working with epoxy resin can be transformative, as each phase, from measuring to application, provides a new opportunity for growth and creativity. This guide has laid the groundwork for you, the beginner, to approach your projects with a professional’s care and expertise. By meticulously following the steps for measuring, mixing, and applying, and utilizing the tips for achieving a bubble-free and flawless finish, you’re well-equipped to tackle a wide range of resin projects.
The key takeaway is that precision, patience, and practice are the pillars of excellence in resin work. As you continue to explore and apply these foundational principles, your skill will invariably evolve. Permit yourself the grace to learn from each project, regardless of the outcome, and know that each mix, each pour, is a step closer to mastering the craft. Your next creation awaits the dedication and passion only you can instill into it. Happy crafting!