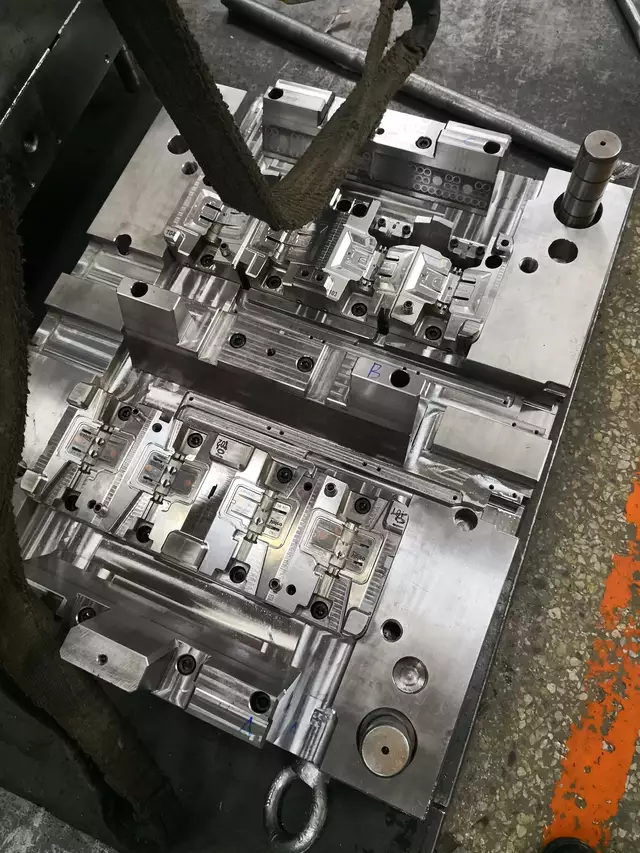
Polycarbonate and ABS are two of the most widely used thermoplastics for injection molded parts and products. But there are important differences between polycarbonate injection molding and ABS injection molding in terms of properties, processing, and end-use applications. This guide provides a detailed overview of each material and injection molding process.
Engineers often select plastics like polycarbonate for their durability and transparency. Companies like PlasticMoulds offer injection molding services for polycarbonate parts suited for demanding applications. ABS plastic is another popular choice for its strength and versatility. PlasticMoulds has expertise in ABS injection molds for automotive, electronic and consumer product components.
Polycarbonate Injection Molding Overview
Polycarbonate (PC) is an extremely versatile engineering thermoplastic valued for its unique combination of toughness, optical clarity, high heat resistance, and dimensional stability. Injection molding is the primary manufacturing process for producing polycarbonate parts and products at scale.
Polycarbonate Material Properties
- Excellent impact strength and ductility even at low temperatures
- Optical clarity and light transmission for transparent components
- High heat resistance (250°F – 300°F heat deflection temperature)
- Dimensional stability and low creep under load
- Wide range of specialty grades (medical, electrical, UV-resistant)
Polycarbonate Molding Characteristics
- Flows readily into complex geometries and thin walls
- Low injection pressures compared to other engineering resins
- Minimal part warpage due to low mold shrinkage
- Excellent mold definition and surface finish possible
- Demolding is easy with low ejection forces
Typical Polycarbonate Applications
- Transparent sheets, lenses, and light covers
- Medical devices and lab equipment
- Electrical components and housings
- Automotive lenses and components
- Riot shields, helmets, and protective gear
ABS Injection Molding Overview
Acrylonitrile butadiene styrene (ABS) is a common thermoplastic known for its strength, stiffness, durability, and wide processing window. It is one of the most injection molded plastics.
ABS Material Properties
- Good strength and impact resistance
- Rigidity and dimensional stability
- Resists stress cracking better than polystyrene
- Variety of colors and customization possible
- Relatively low cost compared to engineering resins
ABS Molding Characteristics
- Excellent flow properties for intricate molds
- Low mold shrinkage minimizes warpage
- Good thermal conductivity allows fast cycle times
- Consistent performance over a wide molding range
- Take note: prone to sink marks in thick sections
Typical ABS Applications
- Consumer appliances and electronics
- Automotive trim components
- Protective equipment like helmets
- Toys, musical instruments, pipe fittings
- Furniture, storage containers, luggage
Polycarbonate vs. ABS: Key Differences
While both versatile thermoplastics, polycarbonate and ABS have distinct differences when it comes to injection molding:
Polycarbonate | ABS |
---|---|
Significantly higher impact strength | Moderate impact resistance |
Optical clarity for transparent parts | Opaque (but easily colored) |
Withstands higher temperatures | Lower heat resistance |
Extremely dimensionally stable | Prone to shrinkage/warpage if not controlled |
Excellent chemical resistance | Can stress crack with certain chemicals |
Higher modulus/rigidity | Slightly lower modulus/more flexible |
Smoother surface finish possible | Slightly more difficult to polish |
Costs more as an engineering resin | Lower cost commodity plastic |
These differences make each material suitable for different applications depending on requirements.
Polycarbonate Injection Molding Design Tips
Optimizing design for polycarbonate injection molding involves considerations like:
- Generous radiused corners and draft angles to aid demolding
- Uniform wall thickness wherever possible to prevent sinks/warpage
- Minimal weld/meld lines since PC has high melt viscosity
- Accounting for molded-in stress that may cause warpage
- Potentially lower clamp tonnage due to low injection pressures
- Appropriate venting for gases since PC is prone to burning
- Entry sprues sized for high melt flow of PC
- Every detail and tolerance possible with PC’s tight process controls
ABS Injection Molding Design Tips
Design tips specific to ABS injection molding include:
- More draft required on walls due to higher friction with tool steel
- Avoiding thick sections prone to shrinkage and sink marks
- Uniform cooling around hot spots to prevent warpage
- Generous fillets and radii required to reduce stress cracking
- Limiting weld lines, especially in high-stress areas
- Tight tolerances on mating/moving components
- Texturing/polishing difficult due to flow lines
- Accounting for higher mold shrinkage in tool design
Typical Defects in Polycarbonate vs. ABS Molding
Each material is prone to certain defects if not molded properly:
Polycarbonate Defects
- Burn marks from overheating, too little venting
- Weld or knit lines from high melt viscosity
- Sinks and voids in areas with thick-thin transitions
- Warpage from residual molding stresses
ABS Defects
- Sink marks in thick sections due to rapid cooling
- Cracking from notches orradii that are too small
- Warpage from non-uniform cooling or shrinkage
- Flashing, shorts, jetting from high melt flow
- Swirl/flow marks that disrupt surface polish
Addressing these defects requires adjusting parameters like temperature, pressure, cooling rate, and mold design.
Secondary Processing of Molded Parts
Both polycarbonate and ABS parts can benefit from secondary operations like:
- Machining – for precision features, holes, threads, fittings
- Laser cutting – for complex geometries unachievable in molds
- Bonding – joining sub-components with adhesives or ultrasonic welding
- Decorating – pad printing, hot stamping, in-mold labeling
- Coating – painting, plating, vacuum metallization, etc.
These secondary processes expand the design possibilities for injection molded polycarbonate and ABS parts.
In Summary: Key Takeaways
- Polycarbonate injection molding allows very high-quality, transparent parts while ABS offers strength at a lower cost.
- Polycarbonate withstands higher temperatures but ABS is less prone to cracking.
- Polycarbonate has extremely low mold shrinkage while ABS shrinkage must be accounted for in tool design.
- Both benefit from generously radiused corners but ABS needs more draft angle on walls.
- Polycarbonate molds require lower pressures; ABS flows readily into thin walls.
- Secondary operations like machining, decorating and coating expand options for both plastics.
Understanding the unique injection molding characteristics of polycarbonate versus ABS ensures you choose the right material for your application and optimize designs accordingly. Both play major roles in molding strong, functional parts at scale.