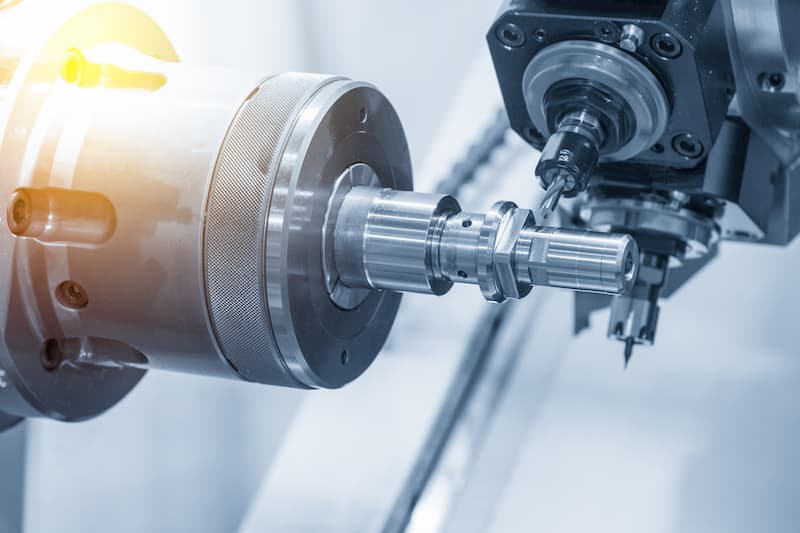
The world of manufacturing grows on accuracy and effectiveness. For producing intricate steel parts, three crucial innovations reign supreme: CNC turning machine, CNC cord reducing machining, and roller passes away. Understanding these processes empowers makers to pick the most appropriate approach for their project needs.
CNC Turning: Shaping Steel With Rotational Reducing
Envision a potter’s wheel, however, for steel. CNC turning, also referred to as computer system numerical control transforming, makes use of a computer-controlled turret to revolve a work surface while a reducing tool exactly gets rid of product. This subtractive production method succeeds at producing cylindrical shapes with numerous functions like grooves, strings, and holes. Here’s a break down of its crucial elements:
Process:
Benefits:
VMC transforming machine deals high precision, repeatability, and surface coating. It’s a rapid and economical option for producing big sets of similar components. Furthermore, CNC lathes can deal with a variety of materials, from soft aluminum to tough steels.
Applications:
CNC turning discovers application in various markets, consisting of auto (shafts, pistons), aerospace (engine elements), and clinical (surgical instruments).
CNC Cable EDM: Precise Machining with a Thin Cord
CNC cord EDM, also called cord disintegration, takes an one-of-a-kind approach to steel cutting. Unlike standard machining that makes use of physical force, wire EDM makes use of a thin, electrically charged cable to deteriorate the work surface material. Here’s a more detailed take a look at this innovative innovation:
Refine:
A continuously spooled cable, normally brass or tungsten, acts as the electrode. The cord takes a trip through an immersed tank of deionized water, a dielectric fluid that does not conduct electricity. High-frequency triggers are released in between the cord and the work surface, triggering local melting and disintegration. The computer system program regulates the wire’s activity, allowing detailed cuts and complicated forms.
Benefits:
CNC wire EDM radiates in developing very thin attributes, sharp corners, and tiny radii that are challenging with standard Mould Machining. It’ particularly beneficial for products that are hard, brittle, or vulnerable to heat distortion.
Applications:
Aerospace components with elaborate cooling channels, clinical implants with delicate features, and mold and pass away making all take advantage of CNC cord EDM’s abilities.
Roller Passes Away: Shaping Steel with Shearing Pressure
Roller passes away use a various method altogether. This steel forming technique uses a collection of contoured rollers to apply shearing pressure and considerably flex the sheet metal right into a wanted form.
Process:
The sheet metal is fed between a set of opposing dies. The rollers have corresponding shapes that gradually change the steel’s account as it passes through. The thickness of the sheet metal and the die design determine the final type.
Advantages:
Applications:
Automotive body panels, device enclosures, and ductwork are archetypes of parts produced using roller passes away.
Choosing the Right Tool for the Work
Picking one of the most ideal strategy depends upon several variables:
Part Geometry:
CNC transforming excels at producing in proportion rotational components. CNC wire EDM takes on detailed shapes with dilemmas. Roller passes away take care of bends and straightforward curvatures in sheet steel.
Material Residences:
profile Roller CNC transforming and wire EDM can take care of a vast array of products. Roller passes away are best suited for ductile sheet metals.
Production Quantity:
Expense Factors to consider:
Roller passes away are typically one of the most cost-effective option for basic shapes and high volumes. CNC turning and wire EDM entail higher configuration costs yet can be cost-effective for complicated components or huge quantities.
Final thought: A Symbiotic Trio
Diamond Machine, CNC wire EDM, and roller passes away are not mutually special. Producers can utilize the strengths of each modern technology to create a total item. For instance, a complicated gear blank might be CNC transformed, with detailed teeth accounts added utilizing cord EDM. Lastly, the gear blank could be roller created to develop a particular flange or other feature.
By understanding the capabilities and restrictions of these techniques, producers can optimize their production procedures, minimize prices, and accomplish exceptional results in the ever-evolving globe of metalworking.