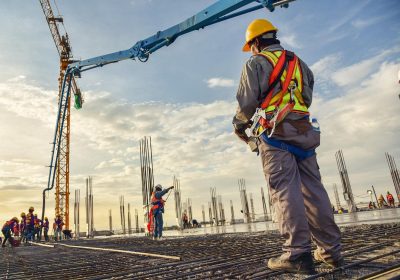
Quality control is the hub that ensures the durability, safety, and functionality of structures in construction. Implementing robust quality control measures is non-negotiable in an industry where precision and reliability are paramount. Hence, from skyscrapers to residential homes, maintaining stringent standards cannot be overstated. In this blog, we will delve into the critical aspects of quality control in construction, exploring its significance and key processes. Furthermore, we will see the positive impact it has on the final outcome of a project.
The Significance of Quality Control in Construction
Quality control goes beyond compliance; it’s about delivering reliable, safe, and functional projects. This process begins with
The Importance of Quality Control in Construction
Safety Assurance
Ensuring the safety of occupants and the public is paramount in construction. Quality control measures identify potential hazards, structural weaknesses, and material defects. Hence, mitigating risks and guaranteeing the structure’s longevity.
Compliance with Regulations
Adherence to local, national, and international building codes and regulations is a non-negotiable aspect of construction quality control. Secondly, by complying with these standards, construction projects gain legal approval and ensure a high level of safety and reliability.
Client Satisfaction
Meeting or exceeding client expectations is a cornerstone of successful construction projects. Quality control measures contribute to delivering projects that align with clients’ visions, fostering trust and satisfaction. Besides this, detailed project specifications and quality standards. Engineers and architects work together to establish clear criteria for construction materials, workmanship, and project deliverables. Rigorous planning is essential to identify potential issues before they arise, preventing costly rework and delays.
Key Components of Effective Quality Control
Material Selection and Testing
The strength and durability of a structure are directly tied to the quality of all the materials used. From steel and concrete to wood and glass, each component must meet stringent standards to ensure the longevity of the building. Further, quality control in material selection involves rigorous testing, documentation, and traceability.
For example, in the case of concrete, quality control measures include testing for compressive strength, slump, and air content. Steel undergoes tests for tensile strength and chemical composition. Wood is inspected for moisture content and dimensional stability. When conducted systematically, these checks guarantee that only materials meeting the specified criteria are utilized, reducing the risk of significant structural failure and ensuring the safety of occupants.
Inspections and Audits
Regular inspections and audits are indispensable components of quality control. These activities involve meticulous reviews of construction processes, specifications adherence, and compliance with safety regulations. Additionally, scheduled and surprise inspections help identify potential issues early in the construction phase. Thus, allowing for timely corrections and preventing the escalation of problems.
Workmanship Standards
Craftsmanship plays a crucial role in the quality of construction. Strict workmanship standards ensure that construction teams adhere to best practices, leading to structurally sound and aesthetically pleasing outcomes. Besides this, training programs and ongoing education for construction teams contribute to maintaining high levels of workmanship.
The Process of Quality Control
Pre-Construction Phase
- Design Review
The foundation of quality control begins with a thorough design review. Ensuring that the architectural and engineering plans are meticulous and accurate sets the stage for a successful construction project. Any potential issues, such as design flaws or material inadequacies, must be addressed before breaking ground.
- Material Selection and Testing
Firstly, choosing high-quality materials is a critical aspect of construction quality control. Regular testing of materials, from concrete to steel, helps identify any discrepancies with specifications. Besides this, it ensures that only materials meeting the required standards are used.
Construction Phase
- Inspection and Testing During Construction
Continuous inspection and testing during construction are essential to catch deviations from the approved plans. This involves monitoring the workmanship, verifying materials on-site, and conducting tests for structural integrity, electrical systems, plumbing, and other critical components.
- Workmanship Standards
Craftsmanship directly impacts the quality of a construction project. Strict adherence to workmanship standards ensures that every aspect of the construction process, from foundation work to finishing touches, meets the desired quality benchmarks.
Post-Construction Phase
- Final Inspection
Before handing over the project to the client, we conduct a final inspection to ensure that all construction elements meet the specified standards. This includes thoroughly reviewing the structure, systems and finishes to identify any defects or issues that need rectification.
- As-Built Documentation
Accurate as-built documentation is crucial for future maintenance and renovations. Quality control extends to documentation. Therefore, ensuring the final plans accurately reflect the constructed reality.
The Role of Technology in Quality Control
Advancements in simple technology have revolutionized quality control in construction. Building Information Modeling (BIM) and construction management software allow real-time collaboration and monitoring. Drones and sensors enable the collection of accurate data, facilitating the identification of potential issues before they become significant problems. Integrating technology into quality control processes increases efficiency, accuracy, and communication among project stakeholders.
Implementing Quality Control Measures
Project Management Software
Firstly, utilizing project management software improves communication and coordination among construction teams. These tools facilitate tracking project milestones, resource allocation, and documentation. Hence, ensuring that quality control measures are systematically implemented.
Training and Education
Investing in the training and education of construction personnel is fundamental to effective quality control. Moreover, keeping teams updated on the latest construction techniques, materials, and safety protocols empowers them to contribute to the project’s success.
Collaboration and Communication
Open and transparent communication between all stakeholders, including architects, engineers, contractors, and subcontractors, is imperative. Therefore, this collaborative effort ensures that everyone aligns with the project’s goals and quality standards.
Preventing Defects and Rework
The financial and temporal implications of defects and rework in construction projects underscore the importance of effective quality control. Identifying and rectifying issues early in the construction process significantly reduces the likelihood of defects. This safeguards the project’s budget and ensures timely project completion. Thus, meeting client expectations and avoiding disputes.
Client Satisfaction and Reputation
Quality control is intrinsically linked to client satisfaction. Delivering a project that meets and surpasses expectations fosters trust and satisfaction. Satisfied clients are more likely to recommend construction firms to others and engage them for future projects. Moreover, a positive reputation built on the foundation of quality workmanship and attention can be a powerful differentiator in a competitive construction industry.
Challenges and Solutions in Quality Control
Variability in Construction Practices
Construction projects often involve various teams with different practices and standards. This variability can lead to inconsistencies in quality. Secondly, implementing standardized processes and conducting regular training sessions can help mitigate this challenge.
Budget Constraints
Striking a balance between adhering to budget constraints and maintaining quality can be challenging. However, cost-effective solutions, value engineering, and strategic planning can help optimize resources without compromising quality.
Technological Advancements
Maintaining technological advancements in construction methods and materials is crucial for effective quality control. Trying innovative technologies, such as Building Information Modeling (BIM) and drones for site inspections, can increase accuracy and efficiency in the construction process.
Conclusion
In conclusion, quality control in construction is not just a box to be ticked; it is the linchpin that holds together the entire construction process. From the selection of materials to the application of cutting-edge technology, every facet of quality control contributes to the creation of structures that endure the test of time. The commitment to delivering excellence not only safeguards the interests of all stakeholders but also improves the reputation of the construction industry as a whole. Navigating the complexities of modern construction, quality control guides us. Hence, ensuring that we don’t just build structures but build them to last. If you are looking for the best quality control service in the construction business, we highly recommend getting in touch with Aegis Construction Services now.