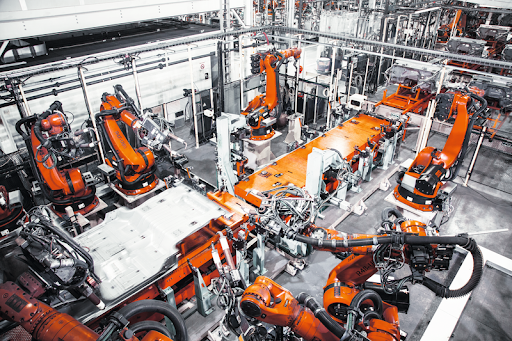
Dominating Accuracy: A Manual for CNC Milling Procedures
Introduction
CNC milling processing remains the zenith of accuracy design, offering unrivaled exactness and flexibility in machining tasks. This article fills in as a complete manual for dominating CNC milling strategies, investigating the complexities of this exceptional assembling process.
Outline
Advancement of CNC milling Innovation
Basics of CNC milling Procedures
Instrument Determination and Advancement
Workpiece Fixturing and Arrangement
Cutting Procedures and Device Ways
High level Applications and Procedures
Background
Conclusion
FAQs
Development of CNC milling Innovation
CNC milling has gone through critical development from manual machining to modern PC controlled frameworks. Headways in innovation have changed CNC milling into an exact and effective cycle, equipped for creating complex calculations with unmatched precision.
Basics of CNC milling Procedures
Apparatus Determination and Enhancement
Choosing the right cutting apparatuses and upgrading their boundaries are essential for achieving ideal outcomes in CNC milling. Factors like apparatus material, math, impact cutting execution, and surface completion.
Workpiece Fixturing and Arrangement
Appropriate workpiece fixturing and arrangement are fundamental for guaranteeing solidity and precision during CNC milling tasks. Sufficient clasping powers, exact positioning, and arrangement limit vibrations and avoidances, bringing about unrivaled machining quality.
Cutting Methodologies and Device Ways
Powerful cutting methodologies and device ways assume an imperative role in improving device life and diminishing machining time. Procedures like rapid machining, trochoidal processing, and versatile processing expand material evacuation rates while keeping up with apparatus trustworthiness and surface completion.
High level Applications and Procedures
CNC milling tracks down applications across different businesses, including aviation, auto, shape making, and prototyping. High level procedures, for example, multi-hub machining, synchronous processing, and 5-hub molding, enable the development of intricate parts with unequaled accuracy and proficiency.
Background
The reception of CNC milling innovation has reformed assembly, empowering organizations to accomplish phenomenal degrees of accuracy, efficiency, and adaptability. Producers put resources into CNC processing hardware and mastery to remain serious in a quickly developing business sector.
Conclusion
CNC milling is the foundation of present day fabricating, offering accuracy, proficiency, and flexibility that are fundamental for delivering top notch parts. Dominating CNC milling strategies enable makers to open additional opportunities in planning, advancement, and efficiency.
FAQs
What is CNC milling, and how can it differ from ordinary processing techniques?
CNC milling includes PC controlled machines that eliminate material from a workpiece to make custom shapes and highlights. Dissimilar to customary processing strategies, CNC milling offers accuracy, computerization, and adaptability in machining activities.
What are the vital variables to consider while choosing cutting instruments for CNC milling?
Factors like device material, calculation, covering, and cutting boundaries impact cutting execution, apparatus life, and surface completion in CNC milling activities.
How do workpiece fixturing and arrangement influence CNC milling tasks?
Legitimate workpiece fixturing and arrangement guarantee steadiness, exactness, and repeatability during CNC milling activities, limiting vibrations and diversions that could influence machining quality.
What are some best in class CNC milling procedures and applications?
High level CNC milling strategies incorporate fast machining, trochoidal processing, multi-hub machining, and 5-pivot molding, which empower the creation of mind boggling parts with accuracy and effectiveness.
How might organizations use CNC milling innovation to upgrade their assembly capacities?
Organizations can use CNC milling innovation by putting resources into cutting edge hardware, enhancing machining cycles, and procuring ability in CNC programming and activity to accomplish more significant levels of accuracy, efficiency, and seriousness.