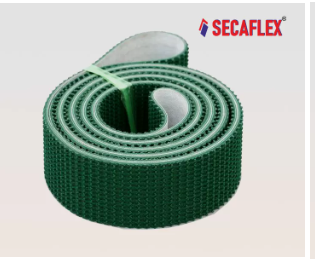
A PU conveyor belt, also known as a polyurethane conveyor belt, is a type of belt used for transporting materials in various industries. It’s made from a material called thermoplastic polyurethane (TPU), which offers several advantages over other conveyor belt materials like PVC or rubber.
Here’s a breakdown of what a PU conveyor belt is and how it works:
Material: Polyurethane, or TPU as it’s often referred to, is a versatile polymer known for its excellent mechanical properties. It combines the strength and durability of plastics with the flexibility and elasticity of rubber. This unique blend makes PU ideal for conveyor belts, offering exceptional:
- High wear and abrasion resistance: This makes PU belts ideal for conveying heavy or abrasive materials.
- Resistance to oils, greases, and chemicals: This allows them to be used in applications where other belts might degrade.
- Good flexibility: PU belts can bend around curves and sprockets without cracking.
- Food-safe options: Certain types of PU are FDA-approved for direct contact with food.
Construction:
- Single-ply or multi-ply: Single-ply belts offer basic functionality, while multi-ply belts have additional layers for increased strength, thickness, or specific properties.
- Smooth or textured surface: Smooth surfaces are good for general conveying, while textured surfaces provide better grip for inclined or wet applications.
- Edge options: PU conveyor belts can have different edge profiles like rounded, V-shaped, or with cleats for added stability.
Working Principle:
- A PU belt runs over a series of rollers or sprockets that drive it forward.
- The material to be conveyed is placed on the belt and moves along with it.
- Depending on the application, the belt can be flat, inclined, or curved.
- Speed and tension are controlled by the conveyor system to ensure smooth and efficient operation.
Applications:
- Food industry: PU belts are widely used in food processing, packaging, and conveying ingredients due to their food-safe options and easy cleaning.
- Pharmaceutical industry: PU belts are used for conveying sensitive materials and medications due to their cleanability and resistance to chemicals.
- Packaging industry: PU belts are used for conveying bottles, cans, and other packaged goods due to their durability and ability to handle uneven surfaces.
- Automotive industry: PU belts are used for conveying parts and components in assembly lines due to their wear resistance and ability to handle oil and grease.
- Textile industry: PU belts are used for conveying fabrics and yarns due to their gentle handling and ability to prevent snags.
What Are The Key Differences Between PVC And PU Conveyor Belting?
PVC and PU are popular materials for conveyor belting, each with its own advantages and limitations. Choosing the right one depends on your specific application.
PVC (Polyvinyl Chloride): A cost-effective, lightweight plastic known for its flexibility and abrasion resistance. It’s suitable for light-duty applications with dry materials at moderate temperatures.
PU (Polyurethane): A more expensive, robust plastic offering superior abrasion resistance, tear strength, and flexibility. It can handle heavier loads, wider temperature ranges, and harsher environments.
Key Differences:
Feature |
PVC |
PU |
Flexibility |
Moderate |
Excellent |
Abrasion |
Good |
Excellent |
Tear |
Moderate |
Excellent |
Weight |
Lighter |
Heavier |
Chemicals |
Moderate resistance |
High resistance |
Cost |
Lower |
Higher |
Food Grade |
Limited options |
Wide range available |
Selecting The Right High-Quality PU Conveyor Belt For Specific Applications.
Selecting the right high-quality PU conveyor belt for your specific application requires considering several crucial factors. Here are some key recommendations to guide you:
- Understand your application requirements:
- Material being conveyed: What type of material will be on the belt? Is it abrasive, sharp, wet, oily, or hot? Different materials require belts with specific properties to resist wear and tear.
- Belt speed and tension: How fast will the belt be moving, and how much tension will be on it? Higher speeds and tensions demand belts with greater strength and durability.
- Conveyor environment: Will the belt be exposed to extreme temperatures, chemicals, or other harsh conditions? The belt material needs to be compatible with the environment to ensure longevity.
- Belt length and width: What are the dimensions of your conveyor system? The belt needs to be the correct size to fit properly and operate efficiently.
- Food grade requirements: If the belt will be used for food contact, it must be FDA-approved and made from food-grade materials.
- Consider the belt properties:
- Thickness: Thicker belts are more durable but may not be suitable for high-speed applications.
- Surface texture: Smooth surfaces are easier to clean but may not offer a good grip for inclined conveyors. Textured surfaces provide better grip but can be more challenging to clean.
- Hardness: Harder belts resist wear better but may be less flexible. Softer belts are more flexible but may wear down faster.
- Color: Consider color for visibility (e.g., white for food applications) or anti-static properties (e.g., black for static-prone environments).
Essential Tips for Extending PU Conveyor Belt Lifespan
PU (polyurethane) conveyor belts offer excellent durability and versatility, but proper care is crucial to maximizing their lifespan. Here are some key tips:
Regularly clean the belt: Remove debris and material buildup, which can cause wear and tear. Use appropriate cleaning methods for your specific material and environment.
Address spills promptly: Avoid allowing spills to harden on the belt, as this can be difficult to remove and damage the material.
Consider scraper blades or self-cleaning systems: These can help automate cleaning and reduce manual effort.
Maintain proper belt tension: Over-tensioning can stress the belt and shorten its life. Under-tensioning can cause slippage and tracking issues.
Regularly check and adjust tension: Follow the manufacturer’s recommendations for your specific belt type and application.
Use tensioners with alarms or indicators: These can help ensure proper tension is maintained.
Inspect the belt regularly: Look for signs of wear, damage, or misalignment. Address any issues promptly to prevent further problems.
Lubricate bearings and pulleys according to the manufacturer’s instructions: This reduces friction and wear.
Store belts properly: When not in use, store belts indoors away from sunlight, heat, and ozone.
The Bottom Line:
PU conveyor belts offer a winning combination of durability, versatility, and ease of maintenance. Whether you’re in food production, manufacturing, or any other industry requiring reliable material handling, a PU belt might just be the perfect solution.