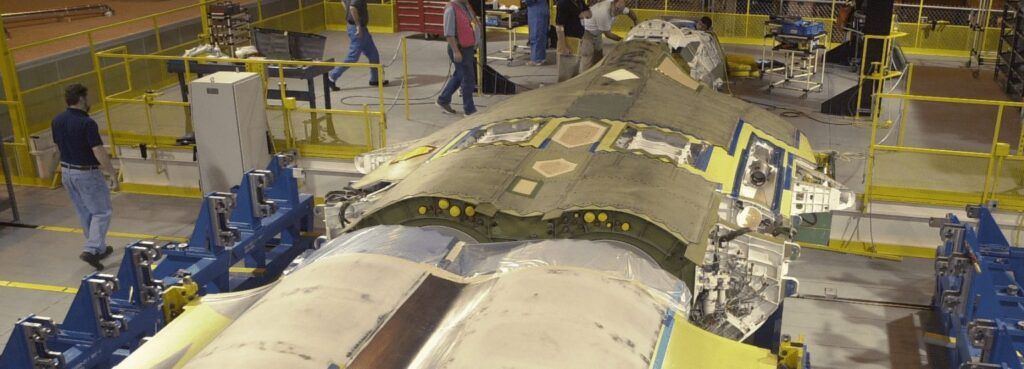
In the complex world of aircraft manufacturing, there are many obstacles to overcome in order to achieve accurate countersink calibration, particularly on parts like the vertical stabilizers of the F-22. This article takes a closer look at the automated countersink calibration process, emphasizing the role of machine vision, and delves into the complexities it addresses to ensure accuracy in the production of F-22 vertical stabilizers.
Introduction
The F-22 vertical stabilizer, with its composite materials and complex design, demands precision in countersink calibration to meet the stringent requirements of modern aviation. This article offers a thorough analysis of the automated countersink calibration procedure, highlighting the difficulties faced and the critical role machine vision played in resolving these issues.
Challenges in Countersink Calibration
- Composite Material Variability:
- Explanation: Composite materials introduce variability that can affect countersink calibration accuracy.
- Solution: Advanced algorithms and real-time measurements are utilized to account for material variations.
- Tolerance Sensitivity:
- Explanation: Countersink depth tolerance requires a high degree of precision that traditional methods may struggle to maintain.
- Solution: Automated systems, driven by machine vision, provide real-time measurements to adjust for tolerance variations.
- Skin Position Tolerance:
- Explanation: The significant difference between skin position tolerance and countersink depth tolerance adds complexity.
- Solution: Machine vision systems enable dynamic calibration, aligning countersinks precisely with the varying skin positions.
- Plunge Depth Dynamics:
- Explanation: The dynamic nature of plunge depth during drilling introduces challenges in maintaining consistency.
- Solution: Automated systems continuously adjust for plunge depth dynamics in real-time, ensuring accuracy across every hole.
- Tool Wear and Resharpening:
- Explanation: Tool wear, especially after resharpening, impacts the accuracy of countersink depth.
- Solution: Automated systems, with machine vision at the forefront, dynamically adjust calibration for each drill bit based on tool wear data.
The Role of Machine Vision: Delta Sigma’s Innovative Approach
Delta Sigma, facing these challenges head-on, has pioneered an innovative approach to countersink calibration, with machine vision taking center stage. The implementation of the Cognix DVT550 smart camera exemplifies the successful integration of machine vision technology.
- Real-time Measurement with Cognix DVT550:
- Delta Sigma employs the Cognix DVT550 smart camera for real-time measurement of countersink depth and positional data.
- The telecentric lens eliminates optical distortion, ensuring accurate measurements even in complex composite materials.
- Calibration During Drill Head Movement:
- Delta Sigma’s approach involves dynamic calibration during the movement of the drill head.
- This real-time calibration ensures precise countersinks, accounting for material variations and dynamic plunge depth.
- Seamless Integration with Motion Controller:
- The machine vision system seamlessly integrates with the motion controller of the drilling machine.
- Calibration data, derived from real-time measurements, is transmitted via an ethernet connection, enabling immediate adjustments.
Conclusion
In conclusion, the automated countersink calibration process, particularly on F-22 vertical stabilizers, presents intricate challenges that demand sophisticated solutions. Delta Sigma’s innovative approach, leveraging machine vision, not only addresses these challenges but sets new standards for precision in aircraft manufacturing. The integration of the Cognix DVT550 smart camera and dynamic calibration during drill head movement exemplify the successful marriage of technology and precision.
FAQs – Frequently Asked Questions
- Q: How does machine vision contribute to precision in automated countersink calibration?
- A: Machine vision, especially through the use of advanced cameras like the Cognix DVT550, provides real-time measurements, ensuring precision in countersink calibration.
- Q: How does the Cognix DVT550 smart camera enhance countersink calibration in composite materials?
- A: The telecentric lens of the Cognix DVT550 eliminates optical distortion, enabling accurate measurements even in complex composite materials.
- Q: Can automated systems using machine vision adapt to variations in skin position tolerance?
- A: Yes, machine vision enables dynamic calibration, ensuring countersinks align precisely with varying skin positions in real-time.
- Q: How does dynamic calibration during drill head movement contribute to precision in countersink calibration?
- A: Dynamic calibration ensures precise countersinks by adjusting for material variations and plunge depth dynamics as the drill head moves.
- Q: What role does tool wear data play in countersink calibration, and how is it addressed by automated systems?
- A: Tool wear data is crucial in automated systems using machine vision, as it dynamically adjusts calibration for each drill bit, ensuring accuracy even after resharpening.