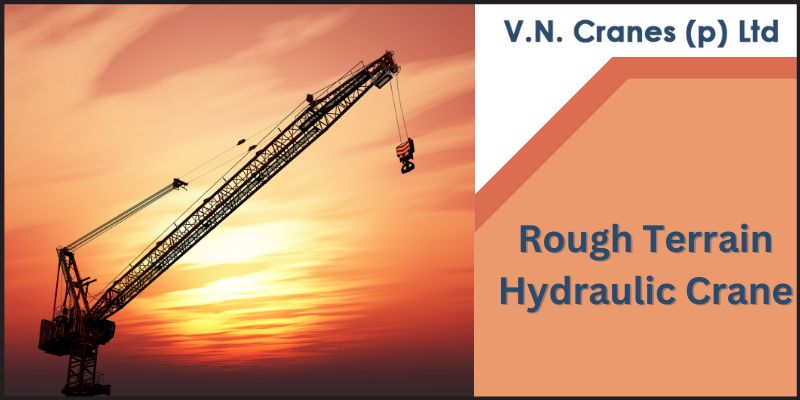
A crane mounted on an undercarriage with four rubber tires that is designed for pick-and-carry operations and for off-road and “rough terrain” applications. Outriggers are used to level and stabilize the crane for hoisting. These cranes offer the perfect combination of power and traction for travel on rutted, muddy job-sites.
These telescopic cranes are single-engine machines, with the same engine powering the undercarriage and the crane, similar to a crawler crane. In a rough terrain crane, the engine is usually mounted in the undercarriage rather than in the upper.
Truck Mounted Hydraulic Crane :
A crane mounted on a truck carrier provides the mobility for this type of crane. Generally, these cranes are able to travel on highways, eliminating the need for special equipment to transport the crane. When working on the job site, outriggers are extended horizontally from the chassis then vertically to level and stabilize the crane while stationary and hoisting. Many truck cranes have slow-traveling capability (a few miles per hour) while suspending a load. Great care must be taken not to swing the load sideways from the direction of travel, as most anti-tipping stability then lies in the stiffness of the chassis suspension. Most cranes of this type also have moving counterweights for stabilization beyond that provided by the outriggers. Loads suspended directly aft are the most stable, since most of the weight of the crane acts as a counterweight.
Crawler Crane:
A crane mounted on an undercarriage with a set of tracks (also called crawlers) that provide stability and mobility. Crawler cranes have both advantages and disadvantages depending on their use. Their main advantage is that they can move around on site and perform each lift with little set-up, since the crane is stable on its tracks with no outriggers. In addition, a crawler crane is capable of traveling with a load. The main disadvantage is that they are very heavy, and cannot easily be moved from one job site to another without significant expense. Typically a large crawler must be disassembled and moved by trucks, rail cars or ships to its next location.
Lorry Mounted Crane :
It is a powerful hydraulic crane mounted on a carrier truck that provides 360 degree solution for loading & unloading. It is an extremely versatile crane that can be utilized for demanding and divergent tasks, such as transporting heavy machinery, erection, delivering building material, plant maintenance, handling pre-fab constructions, installations jobs, maintaining rail roads, timber transportation etc. The major advantages of the crane is as follows:
Vehicle & crane need not mobilize separately, this reduces need for scheduling of vehicle and crane. In other words, as the material to be lifted or dropped is on the lorry crane itself, you don’t require separate vehicles to do the work.
Working range of crane is reduced and set-up time required is minimum, this improves productivity, safety and lead times.
As operations are faster, productive utilization of vehicle and crane increases drastically.
Space taken up during operations is kept to a minimum enabling other operations to be carried out simultaneously in the same area.
Forklift :
It is a powered industrial truck used to lift and transport materials. An important aspect of forklift operation is that most have rear-wheel steering. While this increases maneuverability in tight cornering situations, it differs from a driver’s traditional experience with other wheeled vehicles. While steering, as there is no caster action, it is unnecessary to apply steering force to maintain a constant rate of turn.
Another critical characteristic of the forklift is its instability. The forklift and load must be considered a unit with a continually varying centre of gravity with every movement of the load. A forklift must never negotiate a turn at speed with a raised load which can result in a disastrous tip-over accident. The forklift are designed with a load limit for the forks which is decreased with fork elevation and undercutting of the load. A loading plate for loading reference is usually located on the forklift.
A typical counterbalanced forklift contains the following components :
Truck Frame – is the base of the machine to which the mast, axles, wheels, counterweight, overhead guard and power source are attached. The frame may have fuel and hydraulic fluid tanks constructed as part of the frame assembly.
Counterweight – is a heavy cast iron mass attached to the rear of the forklift truck frame. The purpose of the counterweight is to counterbalance the load being lifted. In an electric forklift the large lead-acid battery itself may serve as part of the counterweight.
Cab – is the area that contains a seat for the operator along with the control pedals, steering wheel, levers, switches and a dashboard containing operator readouts. The cab area may be open air or enclosed, but it is covered by the cage-like overhead guard assembly. The ‘Cab’ can also be equipped with a Cab Heater for cold climate countries.
Overhead Guard – is a metal roof supported by posts at each corner of the cab that helps protect the operator from any falling objects. On some forklifts, the overhead guard is an integrated part of the frame assembly.