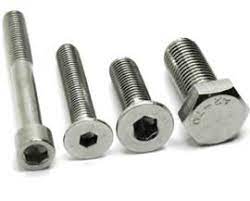
In fasteners, reliability, corrosion resistance, and strength are paramount. Stainless Steel 316 (SS 316), a marine-grade alloy, emerges as a standout choice for fasteners due to its exceptional durability and resistance to harsh environments. This blog explores the unique features, manufacturing processes, and diverse applications of SS 316 fasteners, shedding light on why they are the go-to solution for many industries.
The Alloy: SS 316 Unveiled
Stainless Steel 316 is a molybdenum-bearing austenitic stainless steel known for its enhanced corrosion resistance, making it particularly suitable for applications in aggressive and corrosive environments. Its chemical composition includes chromium, nickel, and molybdenum, imparting a robust combination of mechanical properties and resistance to pitting and crevice corrosion.
Manufacturing Excellence
The production of SS 316 fasteners involves precision and adherence to stringent standards to ensure optimal performance. Key manufacturing processes include:
Material Selection –
SS 316 is chosen for its superior corrosion resistance and durability. The raw material is carefully inspected to meet the required specifications.
Cold Heading –
Cold heading transforms the raw material into the desired fastener shape. This method enhances the mechanical properties of the material, ensuring strength and reliability.
Heat Treatment –
Heat treatment is applied to SS 316 fasteners to optimize their hardness and mechanical strength. This step is crucial for achieving the desired toughness and corrosion resistance combination.
Surface Finish –
The fasteners undergo surface treatments such as passivation or coating to enhance their corrosion resistance and appearance.
Applications Across Industries
Marine and Coastal Structures –
Thanks to their resistance to chloride corrosion, SS 316 fasteners are the preferred choice for structures exposed to saltwater environments, such as marinas, docks, and coastal infrastructure.
Chemical Processing –
In chemical plants where exposure to corrosive substances is inevitable, SS 316 fasteners provide a reliable solution, ensuring the integrity of connections.
Medical Equipment –
The biocompatibility and corrosion resistance of SS 316 makes it suitable for fasteners in medical equipment, where hygiene and durability are critical.
Oil and Gas Industry –
SS 316 fasteners are vital in the oil and gas sector, offering resilience in environments exposed to corrosive substances and high temperatures.
Conclusion
Stainless Steel 316 fasteners are a testament to the marriage of advanced metallurgy and precise engineering. As industries demand fasteners that can withstand the harshest conditions while maintaining structural integrity, SS 316 emerges as a reliable and durable choice. Whether beneath the waves or in the heart of chemical processing plants, these fasteners prove their mettle, securing connections and contributing to the longevity of structures and equipment across diverse sectors. The legacy of SS 316 fasteners lies in their ability to uphold strength and resilience, reinforcing the foundation of industries worldwide.