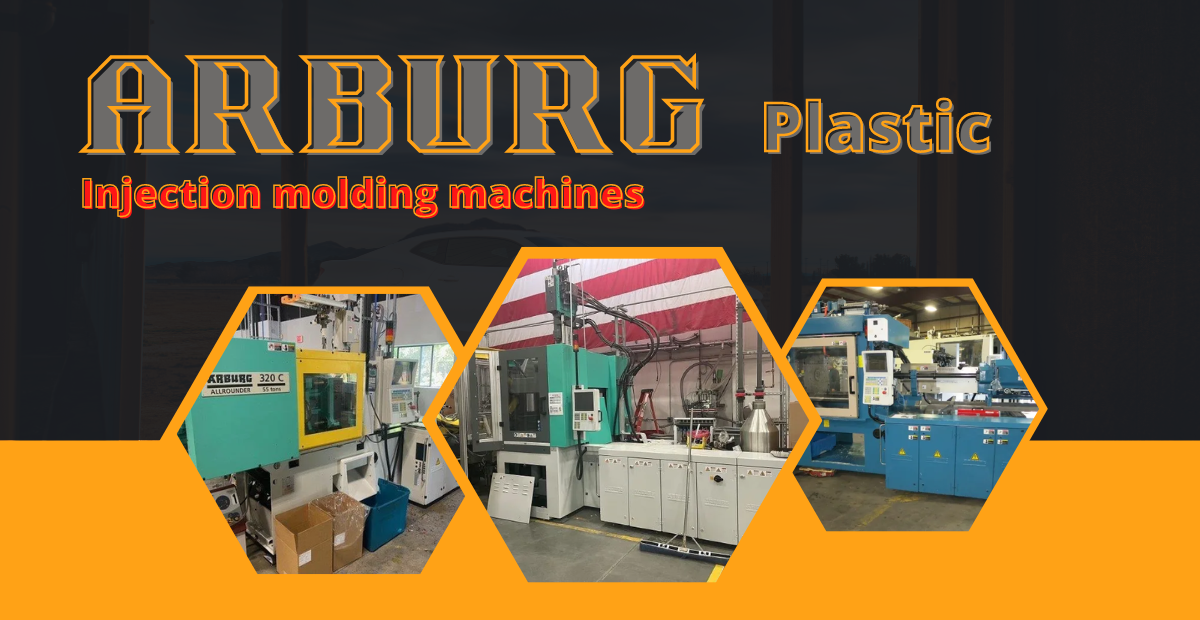
Injection molding machines are an indispensable component of the plastic manufacturing process. These machines are responsible for heating, melting, and reshaping raw plastic material into the desired form of the product. Given its crucial role in the production process, the injection molding machine is rightly regarded as a cornerstone of the plastic industry.
Injection molding machines are essential for the manufacturing industry. However, they can be quite expensive to invest in, with a price range of $30,000 to $80,000. The cost can even go higher depending on the capacity of the machine. Despite the high cost, these machines are crucial for mass production and are designed to produce high-quality products efficiently.
Arburg has carved a niche for itself in the market of injection molding machines owing to its exceptional quality and reliability. As a result, many manufacturers prefer to opt for Used Arburg Injection Molding Machines because of their cost-effectiveness and immediate installation capabilities, which can save both time and cost for the manufacturer. These used machines are an excellent option for those looking to scale up their production capacities without incurring high investment costs. Here’s why an injection molding machine is crucial in production:
How Does An Injection Molding Machine Work?
The process of injection molding involves the use of various crucial components, each with a specific function. These components work together to produce a high-quality product that meets the manufacturer’s requirements. Without the proper functioning of all of the components, the injection molding machine would fail to deliver the desired outcome.
- Hopper: One of the first components is the hopper, which is where the raw material, typically in the form of pellets or granules, is fed into the machine.
- Barrel: Once the raw material is in the hopper, it’s time for the barrel to go to work. The barrel contains a reciprocating screw, which is responsible for melting and homogenizing the raw material. To achieve this, the barrel is heated to maintain the material in a molten state.
- Injection Unit: Next is the injection unit, which is made up of the screw, nozzle, and injection plunger. The screw rotates and moves forward, pushing the molten material through the nozzle and into the mold cavity with high pressure. The clamping unit holds everything in place during the injection process. It consists of a stationary platen and a movable platen, which are brought together to close the mold securely.
- Mold: The mold is the essential piece that defines the shape and features of the final part. It’s made up of two halves: the cavity side, where the part is formed, and the core side, which creates voids and features within the part.
- Cooling System: Finally, the cooling system comes into play. After the material is injected into the mold cavity, the cooling system helps to rapidly cool and solidify the part. This process allows for efficient cycle times.
The Injection Molding Process:
- Material Preparation: With plastic injection molding, the process begins with material preparation, where the raw material is carefully fed into the hopper and conveyed into the barrel. Once inside, the material is heated and melted by the reciprocating screw, which moves back and forth to ensure even heating.
- Injection: Once the material reaches the desired temperature and consistency, the screw moves forward, injecting the molten material into the mold cavity under pressure. This injection process must be carefully controlled to ensure that the material fills every corner of the mold cavity while avoiding any air pockets or other defects.
- Cooling: After the mold is filled, the cooling system activates to rapidly cool the material, solidifying it into the desired shape. This cooling process is critical to ensuring that the final product is of high quality and free from any defects that could compromise its functionality or aesthetics.
- Ejection: Once the part has cooled and solidified, the mold opens, and the finished part is ejected from the mold cavity. This ejection process must also be carefully controlled to ensure that the part is not damaged or distorted in any way as it is removed from the mold.
- Repeat: Finally, the process repeats for each cycle, with the mold closing, material injected, cooled, and parts ejected in a continuous loop. This repetition allows for high-volume production of high-quality plastic parts that meet the exact specifications of the customer.
Conclusion
The process of creating plastic products requires the use of precise and efficient machinery. One such machine that is crucial to this process is the injection molding machine. If you are in the market for one of these machines, it is highly recommended to consider purchasing Used Arburg Plastic Injection Molding Machines. This top-of-the-line brand is well-known for its reliability and quality, making it an ideal addition to any production line. By opting for a used machine, you can save both time and money, provided that you find a reputable seller who can provide you with a well-maintained machine that meets your specific requirements.